SAGE Automation collaborated with CDS, mechanical partner Macweld Industries, the University of South Australia and Nukon to design an Automatic Redemption Terminal (ART) which automates the sorting of containers to a high level of accuracy, while also providing a refund point for customers.
To provide an end-to-end solution for depots, a solution was also needed for the cash redemption and container counting side of the process.
The development of the solutions required a multi-step approach:
- Research and development of customer and depot-facing solutions
- Proof of concept and rapid prototyping
- Development of secure IoT cloud solution
- Manufacture and testing of the solution
- Development of remote monitoring and support
- Deployment of the first iteration
- Development of training materials and an online depot operator training platform
- Continuous improvement of the final design and a multilevel support solution.
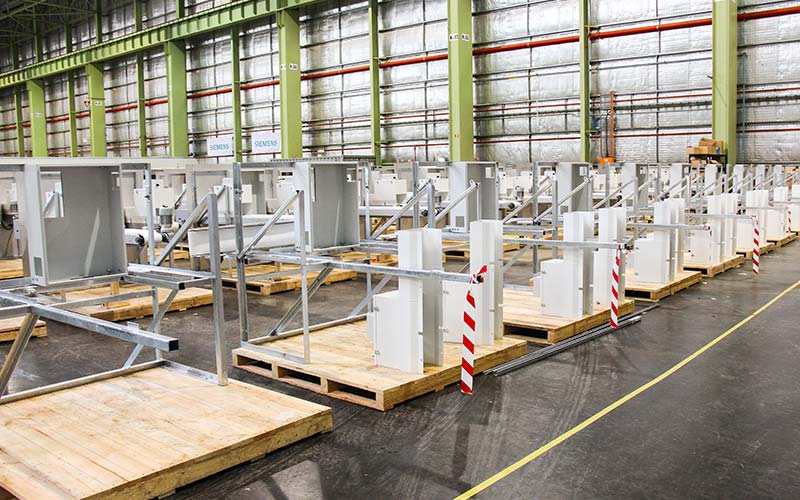
Research and development
SAGE Automation worked with CDS and professors from the University of South Australia (Uni SA) to develop an Automatic Redemption Terminal (ART) for the automated sorting, counting and processing of deposit legislation containers.
The terminal uses a unique smart vision system, developed by Uni SA, to identify the types of containers, including those which have damaged labels.
As sister companies, SAGE and Nukon worked together on the delivery. While SAGE delivered the control systems, Nukon took care of the IT and customer-facing solution, utilising Industrial Internet of Things technology.
Making use of inexpensive computers, Amazon Web Services (AWS) and Internet of Things (IoT), the cloud infrastructure ensured costs were kept down, allowing the system to be easily expanded where needed.
Read more about Nukon's solution here: IoT provides answer to War on Waste
Proof-of-concept and prototyping
As a brand new solution, the idea underwent a proof-of-concept and rapid prototyping phase to ensure it would enable the return of bulk containers in any condition.
The final solution is a secure, robust, cost-effective alternative to reverse vending machines.
Working with Uni SA and Macweld Industries, and following an agile project delivery method, SAGE and Nukon were able to reduce development costs and the client was given opportunities to review, test and adjust the solution during the prototyping stage.
New features were added even after the solution went live, via remote updates and enhancements. This allowed CDS to respond quickly to customer feedback and new challenges.
Supply chain, scalable manufacturing and testing
Working with the SAGE Group of companies provided the opportunity for CDS to access industry knowledge and technology solutions, such as Siemens, Advantech and Beckhoff, as part of the product development process.
SAGE Automation are able to source components from their own supply chain to ensure all terminals are maintainable, and the hardware products used in the design are fit for purpose.
As part of the product development process, SAGE Automation ensured CDS could scale the manufacture of machines as required, enabling rapid expansion particularly as new container deposit schemes are launched in other states.
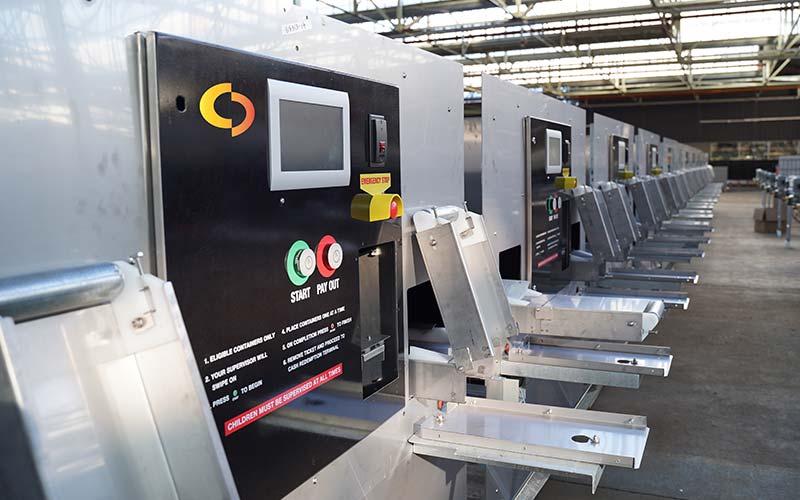
Assembly
While SAGE manufactured the ART control systems in their Tonsley Manufacturing Centre, there was also a requirement to do final assembly and factory acceptance testing prior to shipping to CDS’s customer sites.
To achieve this capability, SAGE expanded into extra manufacturing space within the Tonsley precinct.
As further container deposit schemes have rolled out, SAGE Group has been able to support this growth and continued innovation.
Deployment
Market demand for the automated recycling solution quickly grew as the Queensland container deposit scheme, Containers for Change, began.
A high volume of control panels was required to meet market demand and to keep production costs low, which required SAGE to reduce the time taken to manufacture the terminals.
A number of opportunities to improve the speed to market were identified:
- Panel cutouts - Using SAGE’s CNC machine to door and gland plate cutouts and backplate holes provide increased efficiency when dealing with high amounts of identical panels.
- Panel cabling - SAGE’s automated cable looming machine reduced the time taken to complete a cabinet back panel by 60%.
- Throughput - Orders of 100 machines can be produced at a time, allowing for volume discounts to be obtained from the supply chain.
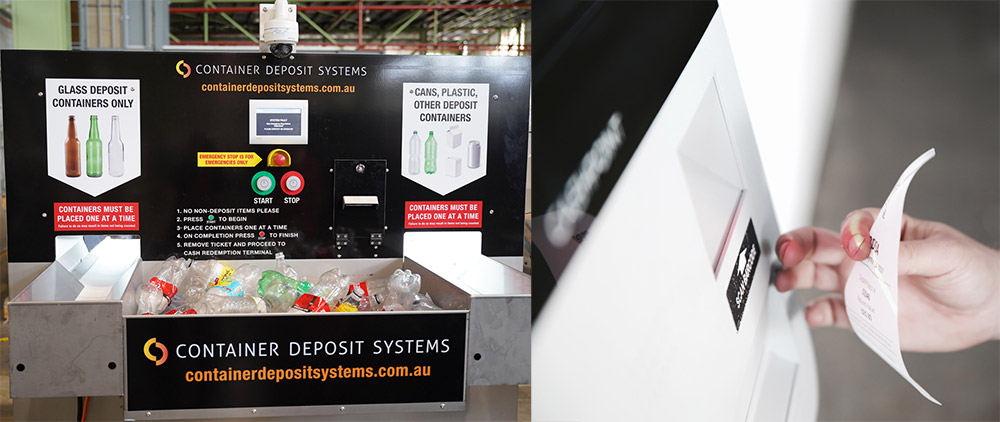
Support
CDS have an ongoing support contract with SAGE Automation and Nukon to ensure smooth operation of technology and that depot managers have 24-hour access to technical support when needed. This model minimises the risk of downtime for depot operators / managers.
SAGE Automation Service in Queensland, WA, NSW and South Australia provide holistic maintenance and support for the depots across Australia. This support includes the machine (such as electrical and mechanical maintenance) and the technology solution implemented.
The service department of each state and territory holds stock of critical spares to provide rapid support in the event of a fault or breakdown.
Nukon Support Desk and the National Operations Centre are critical to enable support as a first point of triage.