The Tasmanian SAGE engineering team designed, tested and implemented the control system for the new cheese vats in just under three months.
“With our extensive experience in the dairy industry we came to them with a recipe management solution. Within that recipe they could alter the parameters to make any kind of cheese they wanted, allowing Ashgrove greater production flexibility,” SAGE Systems Engineer Matthew Scavone said.
“We began the project by writing a comprehensive functional description with a flexible recipe sequence that also covered the other functional aspects of the facility such as the site services and Clean-in-Place (CIP) sequences.”
A non-SCADA solution (HMI only) had to be implemented due to the facility’s set up, scale and budget. The solution included: a full batch recipe system with batch reporting, automation of service equipment, and HMI design with an innovative recipe management system to handle hundreds of unique recipe parameters.
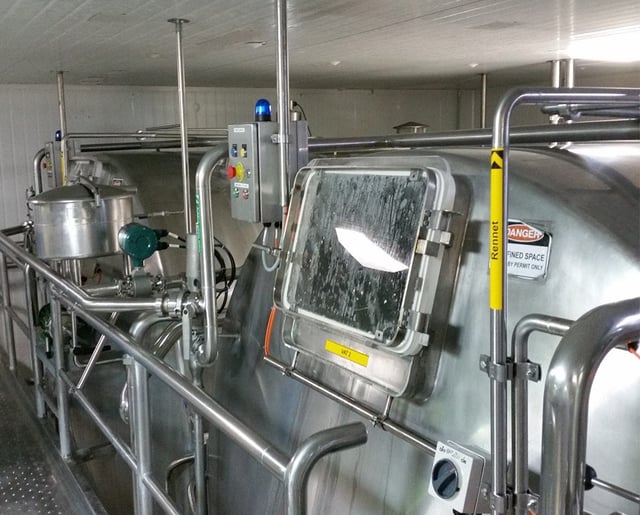
Automation technologies used: Allen Bradley PanelView 1000, Allen Bradley ControlLogix PLC, Allen Bradley SLC 500 PLC.
SAGE delivered an end-to-end solution including project management, design, construct, testing, commissioning and service:
• Estimation, cost planning and procurement
• Safety assessment and management
• Risk mitigation planning and management
• Safety management and environmental assessment
• HMI and PLC system design
• PLC networking, HMI and System Integration
• FAT and SA
• Provision of final, as built, documentation and user manuals
• Ongoing SAGE Service Support and SLA