Project stakeholders:
- Augility/JLL - Department of Defence's Project Manager and Contract Administrator
- Tiwi Partners - Principal Contractor
- AECOM - Department of Defence's design service consultant
- Department of Defence - Fuel Services Branch
- Royal Australian Air Force (RAAF).
Project management and stakeholder collaboration
The project took place over a period of 18 months, with all project partners committed to alignment with the schedule.
One of the major contributors to managing the operational risk involved in the upgrade was the development of a capability matrix outlining what functionality would be available, aligned to a period within the schedule.
During the development of the matrix, input was obtained from multiple stakeholders to ensure it was accurate and achievable; this included gaining an in-depth understanding of how the existing control system functioned during normal use and fault conditions.
System design
SAGE Automation worked with AECOM, the design consultants, for the control panel switchboards, to finalise the layouts and produce the final design based on requirements of Fuel Services Branch.
Both fuel farms required the following functionality as part of the control system:
- Fuel Management System to monitor movements of fuel and data from the tank gauging equipment
- An automated tank gauging system to monitor tank levels
- Level protection for the storage tanks to prevent safe levels being exceeded
- Emergency shutdown systems.
To meet project deadlines, control system development of the PLC and SCADA system was shared between SAGE’s Darwin and Melbourne offices.
Software Factory Acceptance Testing was conducted to ensure functionality required in accordance with the capability matrix was sufficiently tested prior to use on site, reducing the potential delay during commissioning when returning capability to service.
Manufacture of electrical panels
SAGE Automation’s manufacturing team delivered the panel design, procurement, build and FAT for the project.
The control system and electrical upgrade required the manufacture of 15 electrical panels, including a hybrid design with a switchboard on one side, and the control system mounted on the other. With a compressed timeline of 14 weeks to complete the FAT of the panels, SAGE deployed two teams of six people, who worked simultaneously across a total of 3198 hours to meet the deadline.
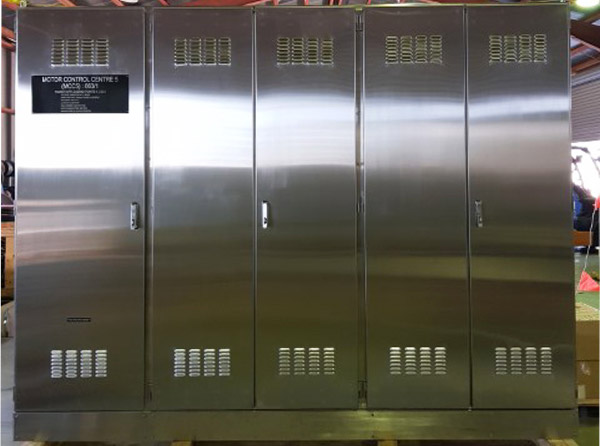
SAGE was responsible for the general arrangement, and aspects of the design to suit existing infrastructure and installation locations. The FAT was completed in Adelaide with the design consultants present (pre-COVID-19).
To complete two panels requiring an upgrade in situ, SAGE’s manufacturing team built the back plates as a replacement of the existing ones. All equipment was prewired and tested prior to shipping to reduce the installation time onsite.
Pre-commissioning
Installation and commissioning took place while maintaining capability in supply to the RAAF, which required an understanding of the legacy control system to ensure effective maintenance and cut-over while the upgraded solution was installed and commissioned.
Commissioning
During preparations for commissioning, a project to extend the control room was running concurrently with electrical installations. The SAGE team worked around the building contractors, modifying hours and space as needed to complete test commissioning and ensure the project schedule could be maintained. With COVID-19 restrictions coming into effect during commissioning, the design consultants were unable to travel to site to witness testing and complete the sign-off. The SAGE project team enabled this to be completed remotely.
Due to the substantial electrical changes required for the upgrade, a Hazardous Areas inspection and audit was required prior to re-energising equipment. SAGE delivered hazardous area inspection and documentation with summary briefs and key installation components inspected remotely due to COVID-19 restrictions.
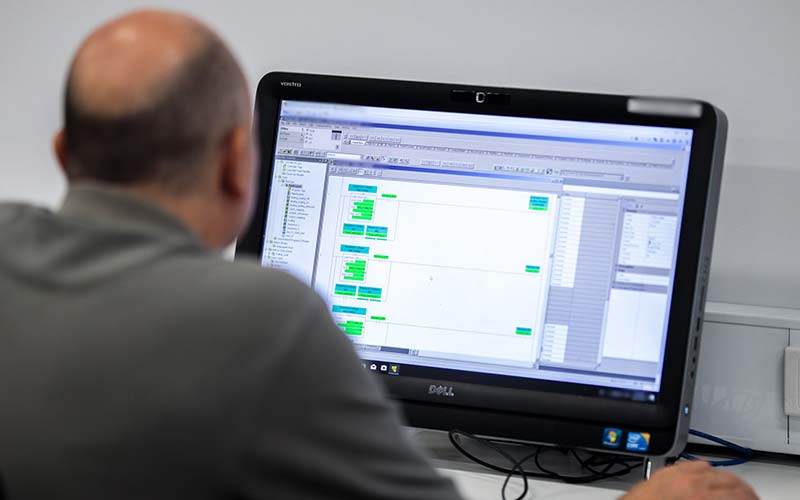
Training
Throughout the project, SAGE Automation’s project manager worked with SAGE Group sister company, Skills Lab, to develop RAAF operator training on the new systems.
Due to COVID-19 restricting travel, the Skills Lab trainer was unable to attend the site to provide classroom-based training, so the materials were adapted and added to a virtual training portal.
Following handover, RAAF operators were able to complete the training via the online training portal.